Current range of Polymer materials
-liquid, 2D film, 3D model
methods for applying chemical cross polymer
-spraying, dipping, soaking
drying methods
-air, oven, freeze -20 Celcius, freeze dry
I am looking for a casting material that will hold surface detail with reduced distortion/shrink rate. Further to this, can we seed the polymer with cells? Can we make a matrix that maintains cell viability? Can the polymer maintain form (and what is the optimum duration) in a growth medium? Can growth be maintained in a bioreactor?
Problems identified in earlier 3D scaffold testing are polymer shrinkage, bulging & distortion and loss of surface detail due to soft consistency before cross linking.
Solution:
-densify polymer
-freeze -20C to minimise shrinkage
-slow down cross linkage by reducing temperature, amount of chemical and dip rather than soak
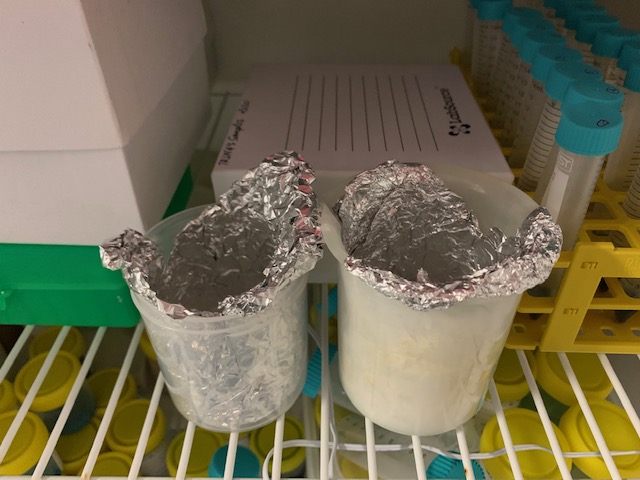
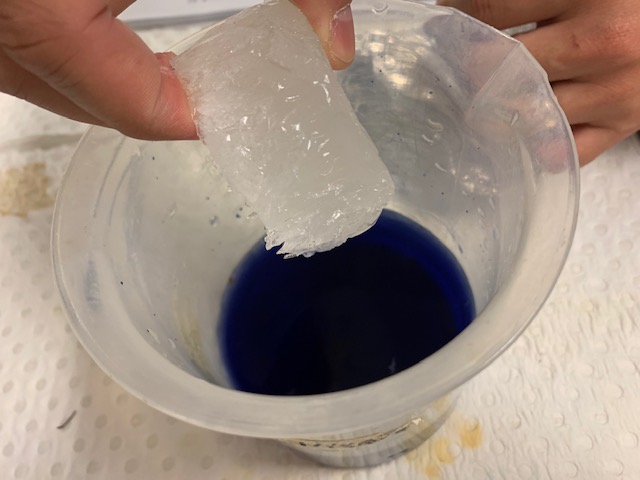
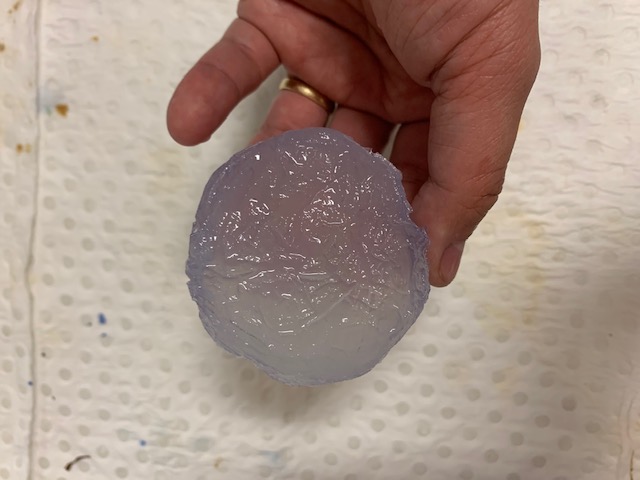
After cross linking in frozen state surface detail and shape are maintained.
Since 2001, human-plant & human-animal hybrids, Chimeras, have manifested in my artworks.
In 2013, I met Andrew Pelling when we participated in the Toxicity bio-art project in Winnipeg Canada. Pelling was showing his work “Repurposed” which included ear shaped apple sculptures supporting human cells. The research article below co-authored by Andrew Pelling might provide insight toward seeding our scaffolds with cells.
Modlevsky et al, Apple Derived Cellulose Scaffolds for 3D Mammalian Cell Culture, journals.plos.org, 2014